3D scanners have firmly established themselves in various industries, greatly simplifying painstaking work. This time Drake helped in the production of spare parts for the metallurgical plant "Cast-Metal" LLC.
Drake faced a difficult task: to help the foundry produce cast iron components: "the snail", “the lid” and "the impeller" (pump elements for concrete mixes). Previously, these parts were purchased in Japan and the delivery time was a whopping 4 months.
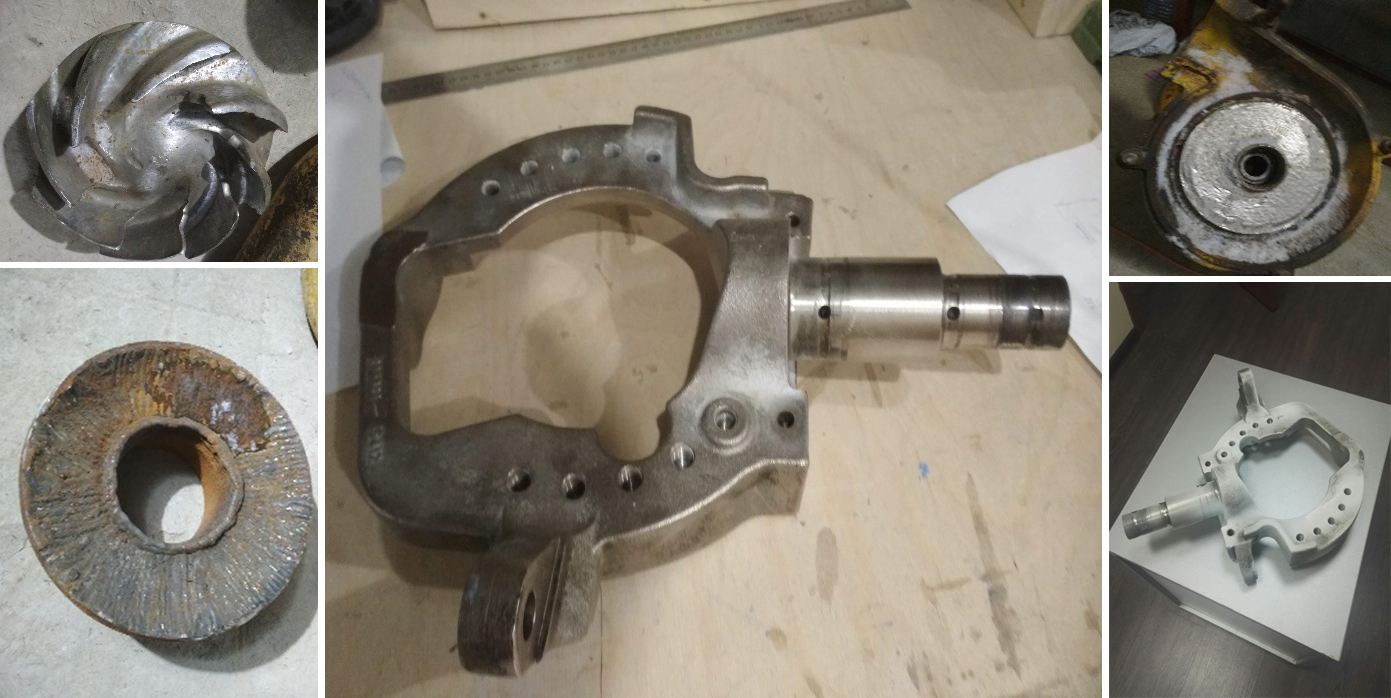
(Cast iron components)
It took Drake Midi 2 minutes to scan the parts, and 5 minutes to create a polygonal mesh for each element. Two more days were spent on postprocessing the data - outstandingly swift compared to months of waiting.
But let’s follow the process step by step. At first, Drake Midi was used to digitize cast-iron parts; this raw data was later turned into polygonal models.
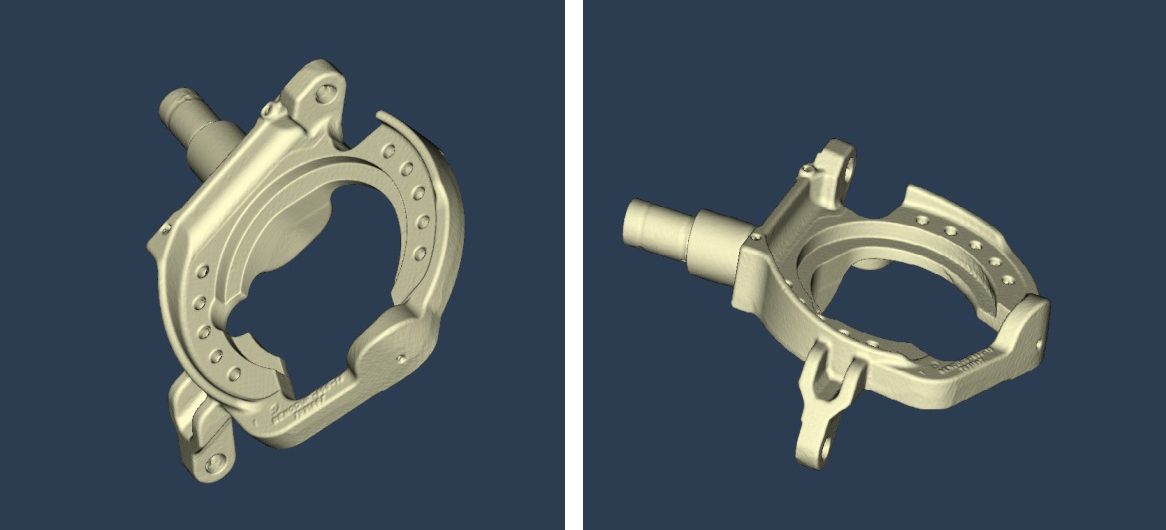
(Polygonal models of the components)
After, that “Cast-Metal” team used the scans to make CAD 3D models. The work took 2 days.
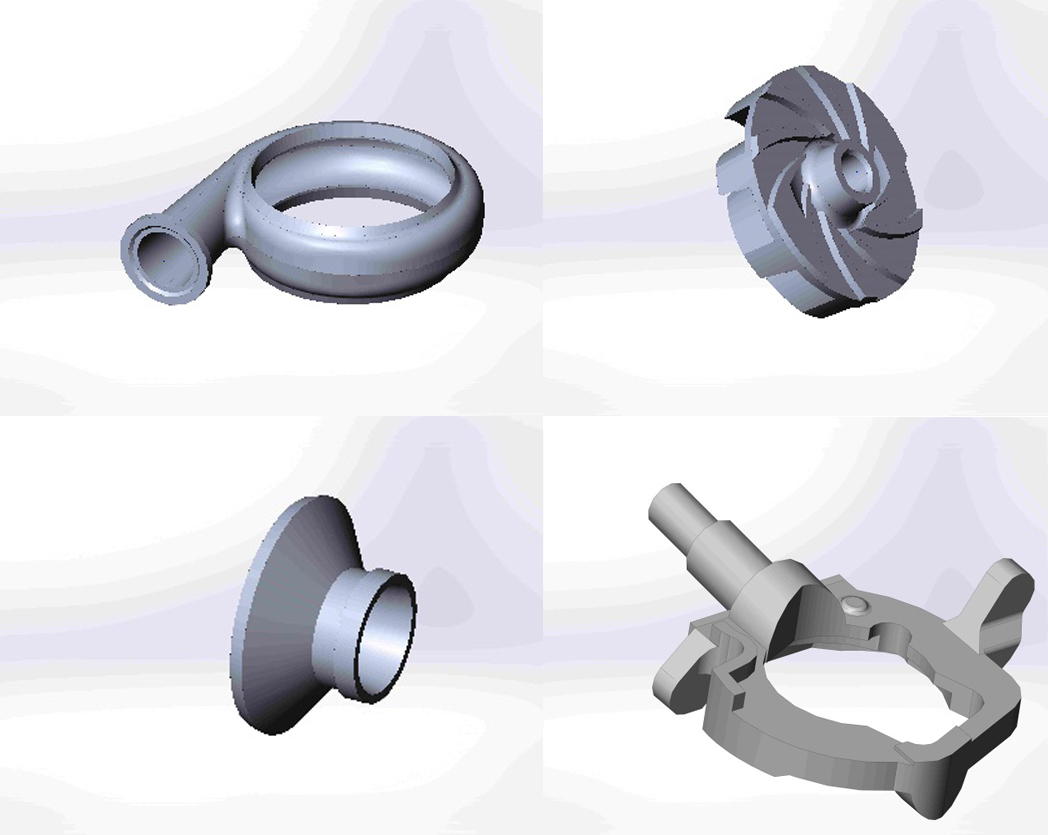
(CAD 3D models made by "Cast-Metal" engineers)
The next stage in the replication of spare parts was the creation of a 3D projection of the casting mold. Measurement accuracy was important up to a millimeter.
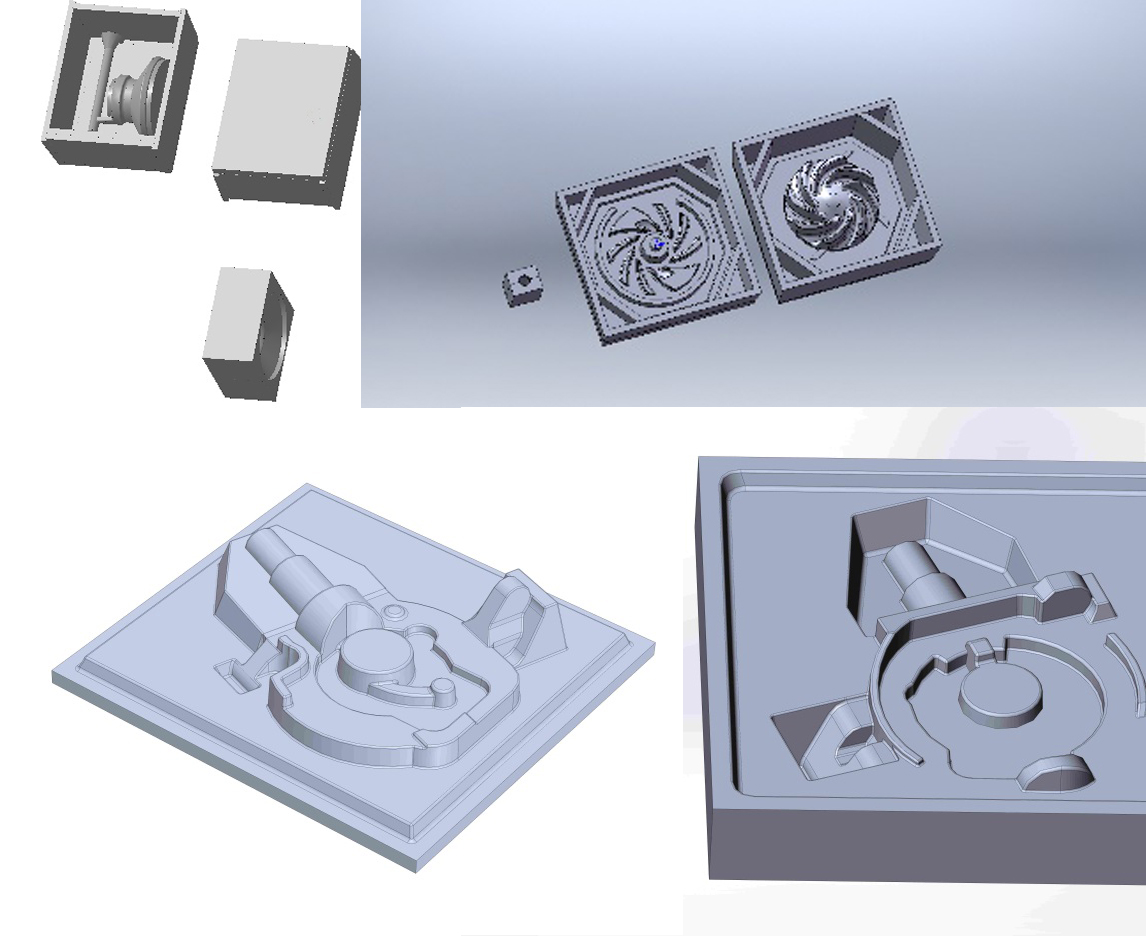
(3D projection of casting molds)
After this, the sand forms were created based on the carved wooden models. The metal was poured into the sand forms; after cooling, the finished elements were cleaned and transferred to the customer. In a couple of days, the replicas were ready.
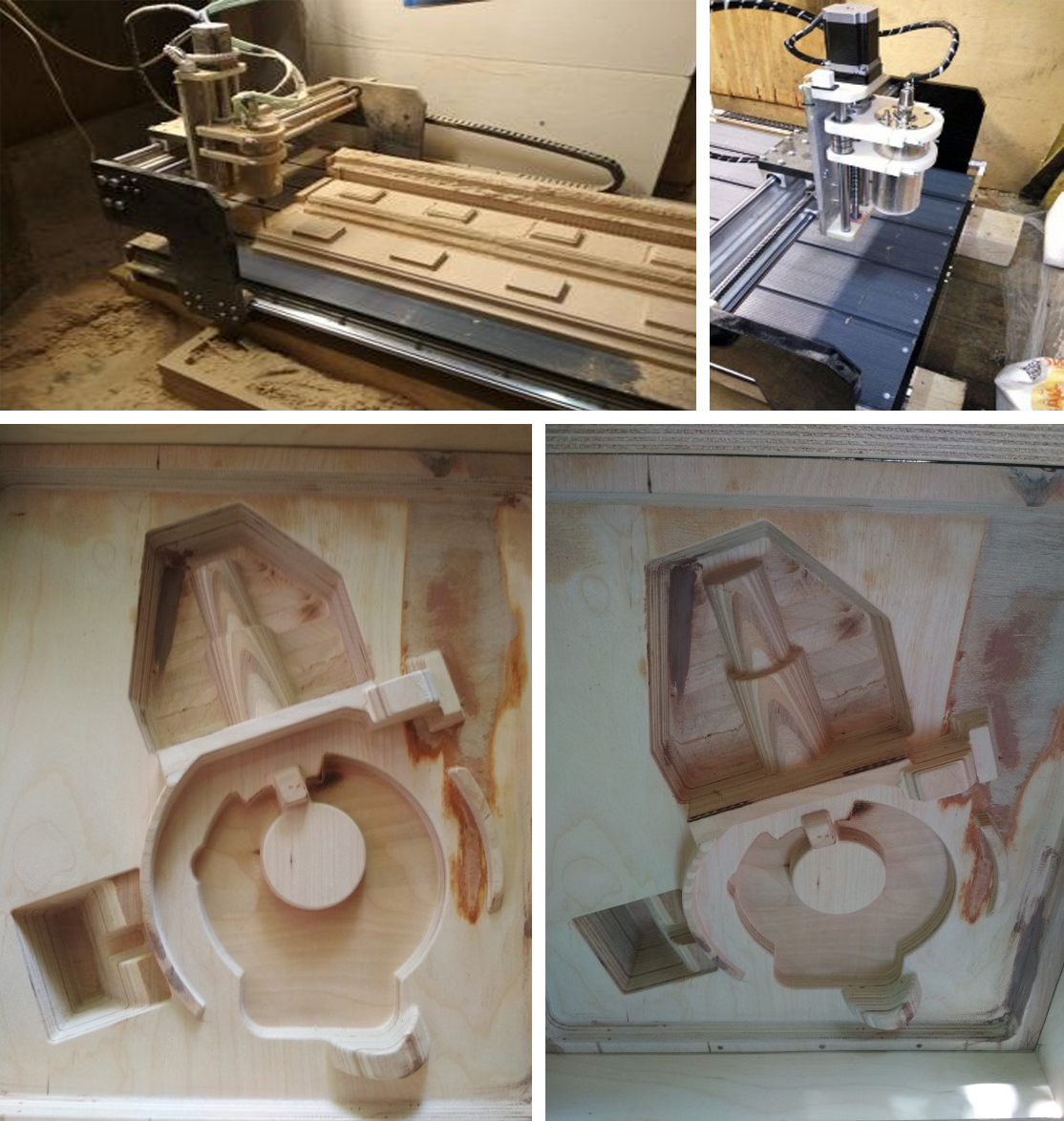
(Making wooden models)
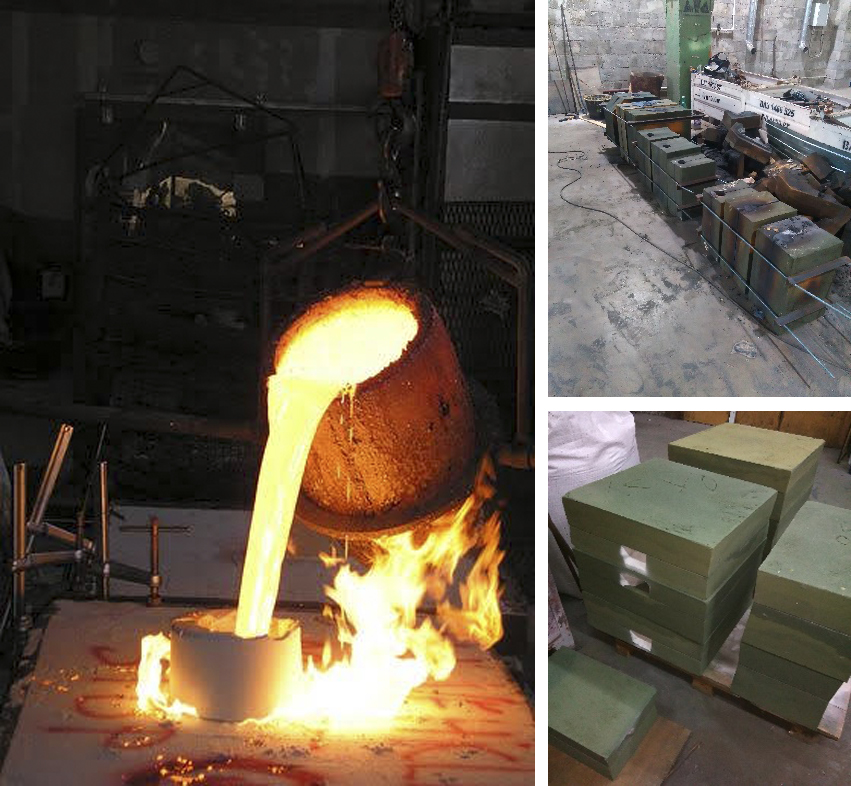