3D scanning technology has become integral across diverse sectors, including healthcare, manufacturing, and entertainment pursuits. With a broad selection of devices available—ranging from mobile to fixed-position scanners, and those with adjustable or static fields of view—choosing the right one can feel daunting. Social media chats and groups often buzz with discussions comparing technologies, brands, and models. This guide aims to simplify the process by offering actionable advice for selecting a 3D scanner tailored to your needs.
Defining Your Requirements
To choose the ideal 3D scanner, start by evaluating your specific needs, environment, and financial constraints. Consider these key questions to guide your decision:
- What are the dimensions and types of objects you plan to scan?
- In what kind of environment will you be scanning?
- How frequently will you use the scanner, and do you need consistent, repeatable results?
- What is the intended use of the scan data, and which software will you use for processing?
- What is your budget range?
In the following sections, we’ll explore how 3D scanner’s function, their key tech characteristics, and provide a comprehensive table to streamline your decision-making process.
How 3D Scanners Operate
3D scanners function similarly to a bat’s echolocation system: they emit a signal, capture its reflection, and construct a digital model based on the returned data. Instead of sound, 3D scanners use light—either laser or structured light (from diodes)—to capture object details. This leads to two primary types of scanners: laser-based and structured light-based.
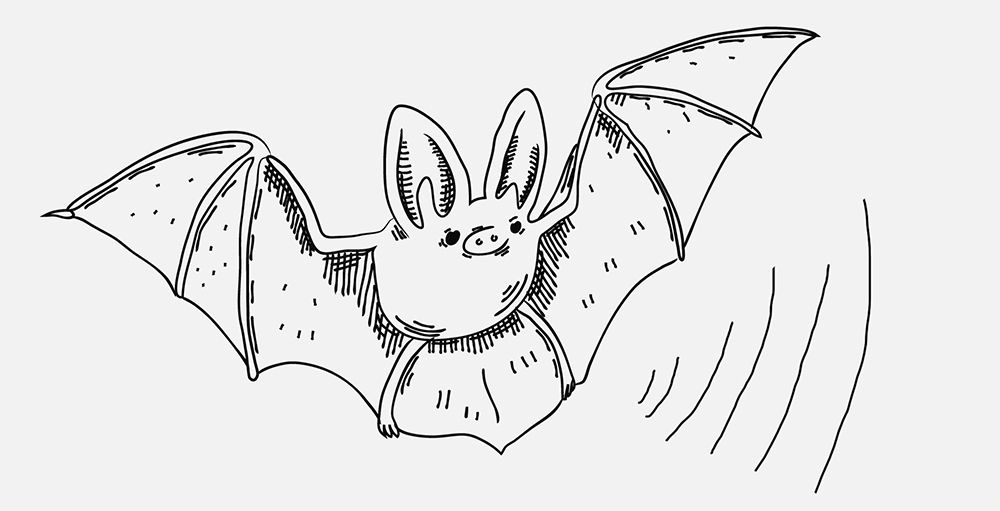
While we won’t delve into the technical intricacies here, if you’re curious about structured light technology, you can explore our article "How does structured light 3D scanning work in Calibry scanners?" The key takeaway is that laser scanners typically excel in applications demanding ultra-high precision, though some lower-end models may produce average results. Structured light scanners, on the other hand, are ideal for applications where extreme precision isn’t critical, yet certain models can still deliver high-quality 3D models suitable for tasks like quality assurance, reverse engineering, or metrology.
Laser Scanners | Structured Light Scanners |
Best for: Quality control, metrology, high-precision works | Best for: Medicine, reverse engineering, prototyping, cultural heritage preservation |
Pros: High precision |
Pros: Accurate, fast capture |
Cons: Slower than structured light, sensitive to reflections | Cons: Can be more tricky to scan dark objects, than for a laser scanner |
Alternative means of making a 3D-scan |
|
Photogrammetry (Camera-Based Scanning) | The process of creating 3D models or measurements from a series of 2D photographs. |
CMM Scanners | The devices use probes or lasers to precisely measure an object's dimensions and geometry, creating accurate 3D digital models. |
Technical Specifications and Features
Selecting a 3D scanner requires careful consideration of its technical specifications. Manufacturers often provide extensive technical details, which can be overwhelming. To make an informed choice, focus on the key features that align with your specific needs. Below, we outline the most critical technical aspects to prioritize when choosing a 3D scanner.
Accuracy and Resolution
Accuracy refers to how closely a scanner’s measurements align with an object’s actual dimensions, while resolution indicates the smallest details it can capture. When comparing scanners using the same technology (e.g., structured light), stationary models typically outperform handheld ones in both accuracy and resolution. If your project demands the highest possible precision, a stationary scanner is often the better choice.
Handheld scanners still deliver excellent scan quality and are well-suited for tasks like reverse engineering, 3D visualization, or quality checks where maximum precision isn’t essential. Factors like portability and user-friendliness may outweigh the need for top-tier accuracy in many cases.
Portability
Scanners differ significantly in portability. Handheld models are lightweight and adaptable, making them perfect for scanning in confined spaces or remote locations, such as digitizing artifacts in archaeological digs or scanning inside narrow structures like pipes. They’re also ideal for objects that can’t be moved, like museum sculptures.
Stationary scanners shine in scenarios requiring high-volume scanning of uniformly sized objects. Pairing them with a motorized turntable can automate the process.
Field of View
The field of view (FOV), also known as the scanning volume, refers to the spatial area a 3D scanner can capture and convert into a digital 3D model. Some stationary scanners allow adjustments to the field of view (FOV) by repositioning cameras or lenses, accommodating objects of varying sizes. For large objects, a wide FOV is necessary, while smaller objects benefit from a narrower FOV. If you want to find out more about the field of view, please read our article "What should we know about the field of view in 3d scanners?"
Software and File Compatibility
A scanner’s hardware is only half the story—software plays a critical role in turning raw scan data into usable outputs. Ensure the scanner’s software is compatible with your intended post-processing tools and supports the file formats you need.
Scanning Algorithms
3D scanners use different tracking methods: geometry (most common), texture, or markers. Scanners with multiple tracking options are pricier but offer greater versatility, enabling you to scan diverse objects. Budget scanners typically rely on geometric tracking, limiting their ability to digitize featureless surfaces, like a car hood. Opting for a scanner with texture and marker tracking expands your capabilities, allowing you to scan flat surfaces (using markers) or intricate textures, such as cultural artifacts like frescoes or paintings. If your work involves complex surfaces, like dark or reflective objects, ensure the scanner can handle these challenges effectively.
A five-question table to choosing a 3D-scanner
Below is a summary table addressing the five key questions to consider when choosing a 3D scanner
Question | Key Considerations |
What size and type of objects will I need to scan? | Determine if you need a scanner with a large field of view (FOV) for big objects or a smaller FOV for detailed, small objects. You may opt for a scanner with a flexible FOV if you plan on scanning objects in varying size range. |
What conditions will I be scanning in? | Assess the environment. Handheld scanners are great for remote spaces, hard-to-reach areas and in all cases when you need portability (e.g., archaeological sites, confined areas). Stationary scanners work best in controlled settings when large volumes of routine scanning are needed and are less suited for immovable objects. |
How often will I scan? How much will my work require standardization? | For frequent, high-volume scanning with consistent results, stationary scanners with automated setups (e.g., turntables) are efficient. Handheld scanners are better for occasional or varied scanning tasks where flexibility is key. |
What will I do with the scan data? What programs will I use to process them? | Ensure the scanner’s software supports your intended use (e.g., reverse engineering, quality control, 3D visualization) and is compatible with your post-processing tools. Check for supported file formats and tracking methods (geometry, texture, markers) for complex objects. |
What kind of budget do I have? |
Budget impacts scanner type and features. Laser scanners offer high precision but are costlier and slower. Structured light scanners are generally more affordable. Budget scanners may only support geometric tracking, limiting versatility.
Affordable scanners will be in the ~$500–$5,000 price range Mid-range scanners - ~$5,000–$20,000 High-End - ~$20,000–$100,000+ |
Choosing the right 3D scanner is a pivotal decision that hinges on aligning the device’s capabilities with your specific needs. By carefully assessing factors such as object size, scanning environment, frequency of use, software compatibility, and budget, you can narrow down the options to find a scanner that delivers optimal performance. Whether you’re a hobbyist seeking an affordable entry-level model, a professional needing versatility for reverse engineering, or an industry expert requiring precision for metrology, understanding key specifications like accuracy, portability, and tracking methods will guide you to the best choice. Use this guide as a roadmap to confidently select a 3D scanner that empowers your projects and drives success in your field.